Possible quality problems and causes of hot dip galvanized steel plate
Taking into account the production process of hot-dip galvanized steel plate and the packaging of finished products, the hot-dip galvanized steel plate may have the following surface appearance defects:
(1) Defects of the original board
The surface defects of the original galvanized plate, such as creases, pits, and wavy edges, continue to affect the galvanized plate and become its surface defects. Therefore, before production, the producer must inspect the original board.
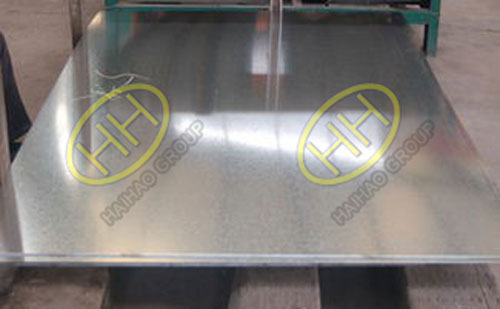
Hot dip galvanized plate
(2) Black spots
- The purity of the galvanized layer is not enough. Metal impurities form a galvanic cell on the zinc surface. When it is beneficial to hydrogen evolution, it is easy to cause black spots on the surface of the zinc layer.
- When the content of impurities such as copper, iron and arsenic in the galvanized layer is high, these impurities appear black after passivation treatment.
- Insufficient treatment of the surface of the original board, forming residues, which makes it impossible to plate zinc on some parts, which causes the zinc coating layer to be defective and easy to fall off, resulting in black spots.
- Leak plating occurs during galvanizing, and black spots are easily formed during post-treatment.
- The residue or small black ash (carbon or carbon compound) in the galvanizing solution adheres to the surface of the zinc layer or resides in the zinc layer, and the zinc layer is firmly bonded. Dark spots can be seen on the finished galvanized plate.
- Abrasion of dark spots. It is caused by rough operation during transportation and stacking.
(3) White rust
The surface of the galvanized steel plate is wet or immersed in rainwater. At a certain temperature, zinc is oxidized to produce white powder. The anti-corrosion ability of the surface with white rust is greatly reduced, which affects its use.
(4) Uneven galvanized layer
The zinc layer on the surface of the galvanized plate is uneven, with uneven thickness, and even small particles on the surface. There is excess zinc liquid on the surface of the strip steel from the galvanizing pot. These excess zinc liquid is blown off with an air knife (jetting high-pressure gas) to control the thickness of the zinc layer. The gas pressure of the air knife, the distance between the air knife and the strip, the speed of the strip, etc. will directly affect the thickness of the zinc layer. If the air knife air supply is unstable or the pressure of the air knife is insufficient, it will cause the accumulation of galvanized layer, that is, zinc scar.
(5) Slag inclusion
There are residues or scum (metallic or non-metallic inclusions) in the galvanizing liquid. Sometimes these slags are included in the galvanized layer. The Shanghai model ship model mechanical model industrial model makes small round spots on the surface, even making the original plate not stained Zinc can easily cause dew point.
(6) Scratches and scrapes, etc.
When the galvanized coil passes through the tension straightener, foreign objects in the straightener cause scratches and scratches on the surface.
(7) Chromic acid scale
In order to improve the anti-corrosion ability of the galvanized steel plate, a very thin passivation layer is formed on the surface of the strip steel, which can be completed by chromic acid treatment, that is, chromization treatment. However, if the chromic acid treatment is poor and there is residual liquid, the surface of the galvanized sheet will appear light yellow bands or stains, or even black spots.