Possible quality problems and causes of electro-galvanized steel plate
Similar to the production process of hot-dip galvanized steel plate, the production process of electro-galvanized steel plate also uses continuous electroplating method, which is divided into pretreatment (cleaning section) and post-plating treatment. The quality of electrogalvanized sheet depends largely on the washing quality before electroplating. The main purpose of post-galvanizing treatment is to improve the surface coating performance and anti-corrosion performance of the galvanized sheet, so as to extend the service life of the galvanized sheet. Post-plating treatment mainly includes phosphating treatment and chromizing treatment. In addition to the original board defects, improper operation of any process will cause quality problems. Common surface defects are:
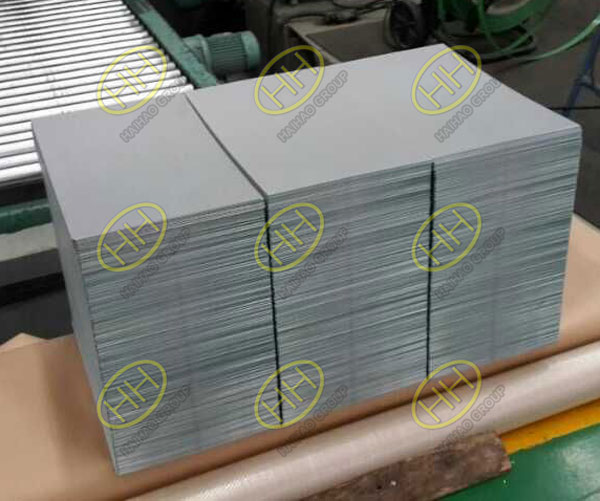
Electro-galvanized steel plate
(1) Pinhole
Refers to the surface of the coating layer is similar to the pinhole chiseled, although the density and distribution are different, but when viewed under a magnifying glass, its size and shape are generally similar. Pinholes are usually defects caused by the adsorption of hydrogen bubbles during the electroplating process. In the electroplating reaction, a large number of bubbles are generated. If these bubbles are not eliminated in time, they will stay between the surface of the steel strip and the anode. The anode and the surface of the steel strip are covered with a gas layer to affect the conductivity, causing the surface of the steel strip to be partially coated .
(2) Pock
Refers to the irregular cavity on the surface of the coating, which is characterized by different shapes, sizes and depths. Pockmarks are generally caused by defects in the substrate or adhesion of foreign objects during the plating process.
(3) Burr (or rough)
It refers to the foreign body with a bumpy feel on the surface of the plating layer, which is usually characterized by being more prominent in the plating direction or the high current density area. The thickness of the zinc layer of electro-galvanized zinc is controlled by controlling the current density and the strip speed, that is, increasing the current density and decreasing the strip speed can increase the thickness of the zinc layer. But this has certain limits. When the strip speed is very low and the current density is high, the surface of the coating will become rough, which will affect the quality of the coating.
(4) Bubbling
Refers to the raised bubbles on the surface of the coating, which is characterized by different sizes, densities and densities, and separation from the substrate. Generally, the zinc alloy and aluminum alloy coatings are more obvious.
(5) Peeling (or shedding)
Refers to cracked or non-cracked defects that are peeled off from the coating and the substrate. Usually caused by poor pre-plating treatment.
(6) Spots
Refers to defects such as color spots and dark spots on the surface of the coating. This is due to poor deposition of metal ions in the plating layer, adhesion of foreign objects or unclean cleaning of the passivation solution after passivation treatment.
(7) Yin and Yang side
Refers to the defects of uneven brightness or uneven color on the surface of the coating layer, and in most cases exhibits certain regularity in similar products.
(8) No local coating
The surface of the plating layer has the defects of leaky plating, exposed iron spots or spots of different sizes and shapes (except for process regulations).
In addition to the above-mentioned surface defects, the coating surface sometimes has damage, scratches, white rust, roll marks, pits, creases, black spots, unwashed salt marks, water marks, erasable or Defects such as brown, brown passivation film and dendritic, sponge-like and stripe-like plating. All these defects will have a certain impact on the use of galvanized plate.