What are the machining methods of stainless steel pipe fittings?
Stainless steel pipe fittings play a crucial role in industrial piping systems, providing superior corrosion resistance, durability, and versatility. These fittings are widely used in sectors such as petrochemical, shipbuilding, food processing, water treatment, and construction.
For high-quality production of stainless steel pipe fittings, various machining techniques are applied based on the shape, size, and intended use of the component. This article explains the six most common machining methods for stainless steel pipe fittings, their advantages, and typical applications.
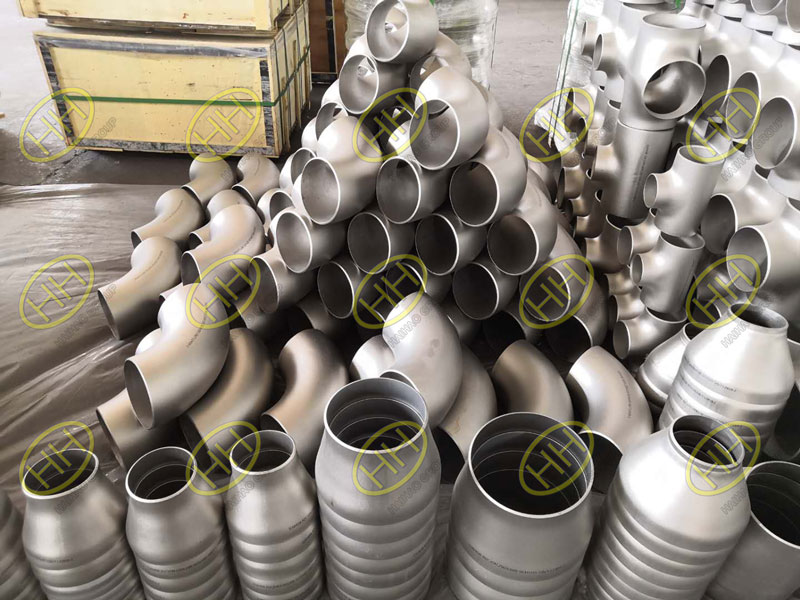
Stainless steel pipe fittings
Key Machining Methods at Haihao Group
Here’s how Haihao Group applies various advanced machining methods to produce our range of stainless steel pipe fittings:
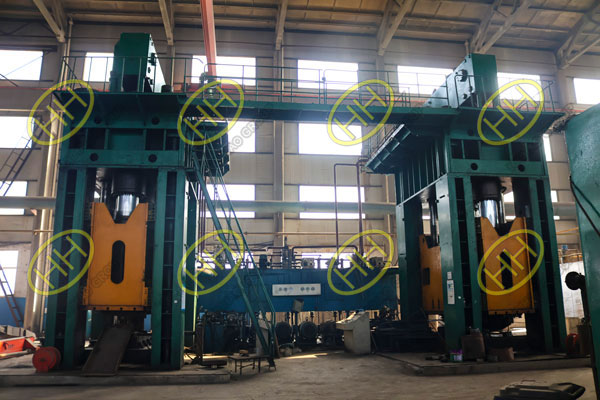
6000 Tons Pressing Machine in Haihao Group
1. Forging and Pressing: Building Fundamental Strength
Forging involves shaping metal by applying compressive forces. For stainless steel pipe fittings, we use powerful forging and pressing machines to reduce the outer diameter of pipe ends or sections, creating a denser, more uniform grain structure. This method is crucial for fabricating heavy-wall and high-pressure fittings, enhancing their mechanical properties significantly. Our precise heat control during forging prevents material degradation and ensures optimal material flow.
Advantages:
- High strength and fatigue resistance
- Ideal for fittings subjected to high pressure or stress
Applications: Elbows, reducers, and tees used in high-pressure pipelines.
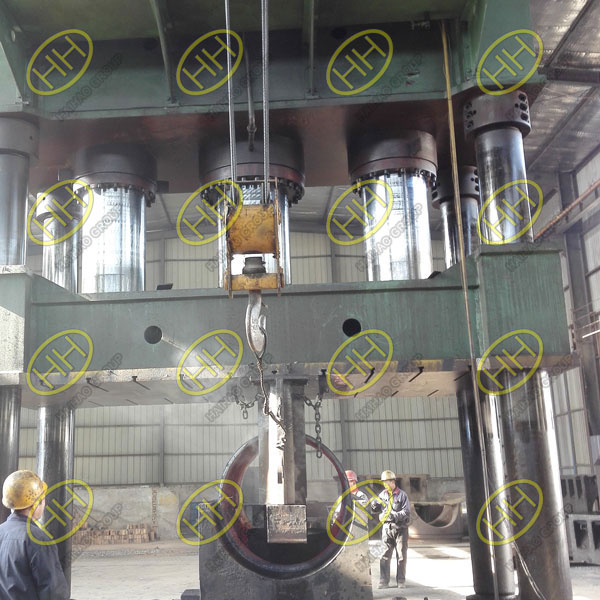
Tee Pressing Machine in Haihao Group
2. The Roller Method: Achieving Smooth Curves and Uniformity
In the roller method, we place a specialized core inside the stainless steel tube. External rollers then apply pressure, gradually shaping the material. This technique is particularly effective for achieving precise roundness and uniform wall thickness, especially for certain reducers or specific pipe end forms. Our operators at Haihao Group are highly skilled in managing the stainless steel’s inherent spring-back, ensuring consistent and accurate final dimensions.
Advantages:
- Smooth surface finish
- Uniform wall thickness
Applications: Long radius elbows, thin-walled pipe fittings.
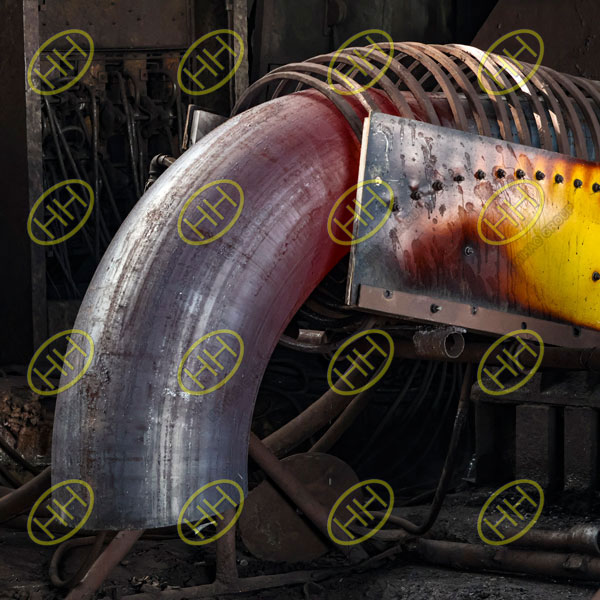
Elbow Bending Machine in Haihao Group
3. Stamping Method: Efficient Shaping for Volume Production
The stamping method utilizes a punch press with a tapered core. This setup efficiently expands the pipe end to achieve the required size and shape. While seemingly straightforward, stamping stainless steel demands carefully designed dies to prevent tearing and maintain consistent wall thickness. Haihao Group engineers leverage custom tooling and optimized pressing parameters, making this method highly efficient for specific standardized fitting geometries.
Advantages:
- Suitable for mass production
- Consistent and repeatable shaping
Applications: Pipe caps, flared ends, flanges.
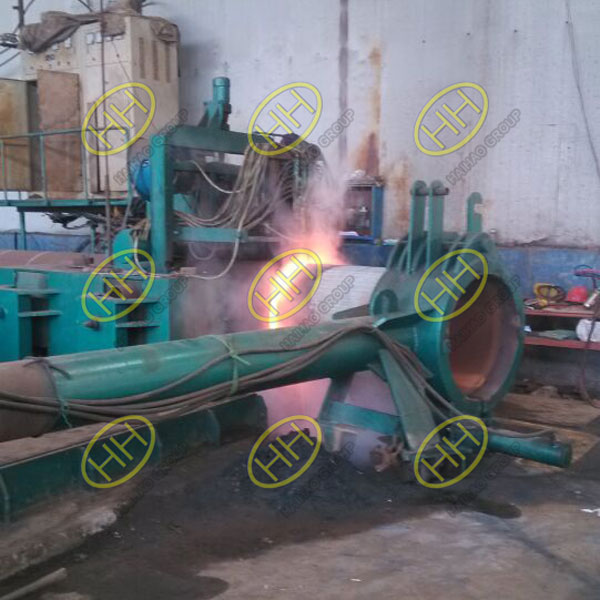
Hot induction bending machine in Haihao Group
4. Bending and Forming: Mastering Complex Angles
For elbows, U-bends, and other angular fittings, bending and forming are critical. We employ several techniques:
Stretch Bending: Material is stretched over a die.
Stamping Bending: Utilizes a punch to form the bend.
Roller Bending: Involves 3-4 rollers (two fixed, one or two adjustable) to precisely bend the pipe.
At Haihao Group, our advanced bending machines are equipped with precise controls to manage the stainless steel’s work-hardening tendencies. We carefully regulate bending speeds and use specific lubrication to ensure smooth curves, minimize material thinning, and maintain strict ovality tolerances.
Advantages:
- Maintains structural integrity
- Suitable for complex angles and radii
Applications: 45° and 90° elbows, U-bends in heat exchangers.
5. Rolling Method (Ring Rolling): For Thicker Wall Uniformity
This method is primarily used for creating heavy-duty pipe rings or seamless, thick-walled segments, often without a mandrel. It’s ideal for producing components that require substantial material thickness and robust construction. Our large rolling mills are operated by experienced technicians who meticulously monitor the process. This ensures uniform wall thickness throughout the stainless steel material, free from internal defects, creating exceptionally strong and uniform sections for the most demanding applications.
Advantages:
- Low tooling cost
- Ideal for heavy-duty fittings
Applications: Large-diameter reducers, couplings.
6. Bulging Method: Precision Expansion with Fluid Power
The bulging method allows us to create complex, expanded shapes. We primarily use two approaches:
Rubber Bulging: Rubber is placed inside the tube and compressed by a punch, forcing the tube to expand into a die.
Hydraulic Bulging: A liquid is filled inside the pipe, and precise hydraulic pressure is applied to expand the pipe into the desired shape.
Haihao Group frequently uses hydraulic bulging for manufacturing seamless tees and caps. This method offers excellent control over material expansion, minimizing thinning and ensuring a superior internal and external surface finish, which is paramount for stainless steel’s performance.
Why Choose Hebei Haihao Group for Stainless Steel Pipe Fittings?
With over 40 years of manufacturing experience, Hebei Haihao Group specializes in producing stainless steel pipe fittings according to international standards such as ASME B16.9, EN 10253, and ASTM A403. Our products undergo strict quality control procedures including material analysis, dimensional inspection, non-destructive testing (NDT), and pressure testing.
We supply fittings for critical industries such as LNG, offshore platforms, chemical plants, and power stations worldwide.
Frequently Asked Questions (FAQ)
Q1: Which machining method ensures the highest strength for stainless steel fittings?
A1: Forging and pressing provide the best strength and grain refinement, ideal for high-pressure applications.
Q2: Can customized shapes be produced?
A2: Yes, hydraulic bulging allows the creation of customized shapes and sizes based on project requirements.
Q3: What materials are available for stainless steel fittings?
A3: Grades such as 304, 316, 321, 347, 904L, Duplex 2205, and Super Duplex 2507 are available depending on the application’s corrosion and temperature requirements.
Choosing the right partner for stainless steel pipe fittings is crucial for your project’s success. At Haihao Group, we combine decades of hands-on experience with cutting-edge technology and an unyielding dedication to quality. From material selection to final inspection, our expert team ensures that every fitting meets the highest standards.
Contact us today to discuss your specific requirements for stainless steel pipe fittings. Let Haihao Group’s expertise be the foundation of your next successful project. Email:sales@haihaogroup.com