What is a socket weld pipe fitting?
When you’re working on a piping system that handles moderate to high pressure, you need a connection method that combines reliable sealing with straightforward assembly. Socket weld pipe fittings offer exactly that balance.
In many projects—especially those involving steam, oil, or chemical lines—socket weld connections are a standard solution for pipe sizes up to 2 inches. Here’s what you should know about them, and how to decide if they’re the right choice for your application.
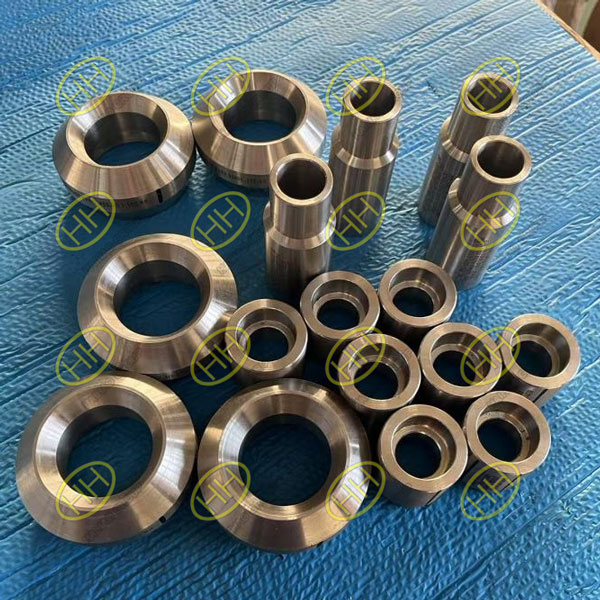
Inconel 625 Socket Weld Fittings ready for shipment from Haihao Group factory
Definition and Basic Design
A socket weld fitting is a forged component with a recessed bore. During installation, the pipe end is inserted into this socket until it bottoms out. A fillet weld is then applied around the perimeter to secure the joint.
This design helps maintain alignment and creates a smooth internal flow path, reducing turbulence. It also allows welders to achieve consistent weld penetration without the need for full beveling as in butt weld joints.
Types of Socket Weld Pipe Fittings:
At Haihao Group, we specialize in manufacturing a full range of socket weld pipe fittings that meet international standards such as ASME B16.11, MSS-SP-79, and JIS B2316. Our socket weld pipe fittings are widely used in high-pressure and high-temperature piping systems across oil & gas, petrochemical, power, and shipbuilding industries.
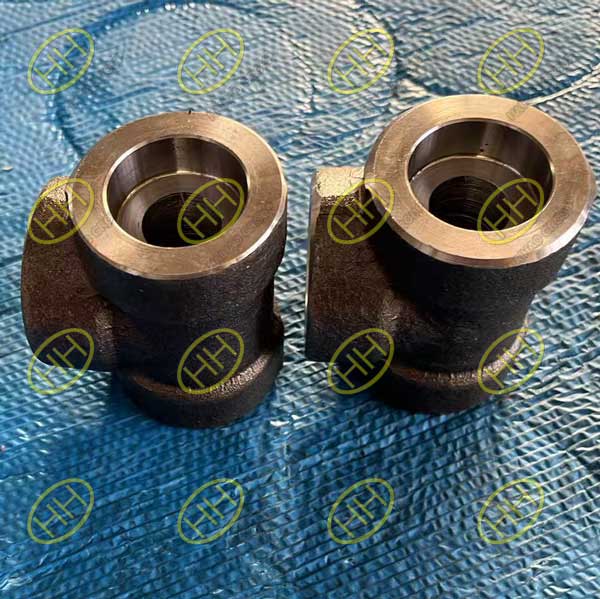
ASME B16.11 ASTM A350 Gr LF2 Cl1 socket weld tees produced by Haihao Group
Here’s a quick overview of the socket weld fittings we can supply:
- Socket Weld Elbows (90° and 45°): Used for directional changes in piping, available in short radius and long radius designs.
- Socket Weld Tees and Reducing Tees: Designed for branch connections in pipelines, with options for equal or reducing branch sizes.
- Socket Weld Couplings (Full and Half): Ideal for joining two pieces of pipe together or for connection to equipment nozzles.
- Socket Weld Crosses: Used in systems requiring four-way pipe intersections.
- Socket Weld Caps: To terminate the end of a pipe or fitting securely.
- Socket Weld Reducers / Reducing Inserts :For connecting pipes of different diameters while maintaining a socket weld joint.
- Socket Weld Unions: Allow for easy disassembly of piping without cutting, suitable for maintenance access.
Why Use Socket Weld Fittings?
Here are a few reasons socket weld fittings remain popular:
- Positive positioning: The socket ensures the pipe is correctly seated before welding.
- Simplified welding prep: Unlike butt weld fittings, you don’t need to bevel the pipe ends.
- Good mechanical strength: A properly executed fillet weld provides excellent resistance to fatigue and vibration.
- Reduced leak paths: Compared to threaded fittings, socket welds eliminate the risk of thread leakage.
- Compact installation: Suitable for confined spaces where butt welds are more challenging.
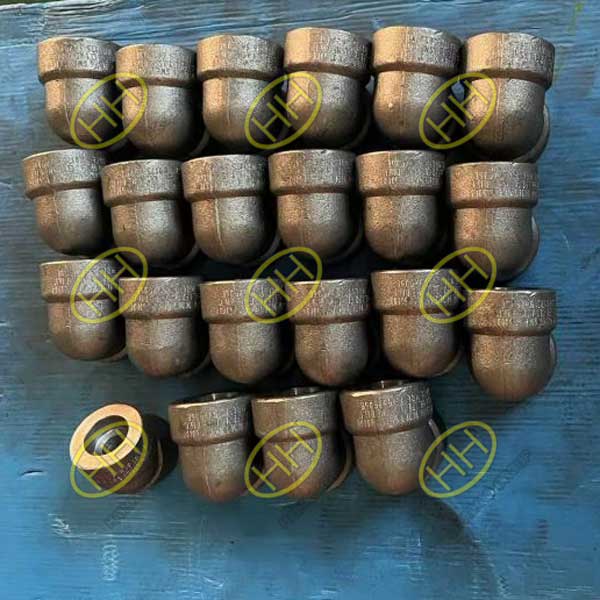
ASME B16.11 90° socket weld elbows A350 GR. LF2 CL1 NACE MR0175 Produced By Haihao Group
Limitations to Consider
Socket weld fittings aren’t perfect for every scenario.
If you’re dealing with piping systems that require frequent disassembly, or if crevice corrosion is a concern (especially with corrosive fluids), socket welds might not be ideal. The small gap between the pipe and the socket can trap fluid residue, which in some cases leads to corrosion over time.
They are also typically limited to pipe sizes NPS 2″ and smaller, due to challenges in welding and inspecting larger diameters.
Common Standards and Materials
The most widely referenced standards for socket weld fittings include:
- ASME B16.11: Forged steel fittings dimensions and tolerances.
- MSS-SP-79: Socket welding fittings for general use.
- JIS B2316: Japanese industrial fittings standards.
You’ll find socket weld fittings manufactured in materials such as:
- ASTM A105 Carbon Steel
- ASTM A182 F304/F316 Stainless Steel
- ASTM A350 LF2 Low-Temperature Carbon Steel
Typical Applications
In our experience at Haihao Group, socket weld pipe fittings are often used in:
- Steam piping systems in power plants.
- Oil and gas process lines.
- Compressed air systems.
- Chemical transfer lines in refineries.
- Hydraulic piping circuits.
For example, on a recent petrochemical project in Southeast Asia, we supplied over 3,000 socket weld elbows and tees in ASTM A105 carbon steel for a high-pressure steam network.
Socket Weld vs. Butt Weld vs. Threaded Fittings
Below is a practical comparison to help you choose the most suitable connection method:
Feature | Socket Weld Fittings | Butt Weld Fittings | Threaded Fittings |
---|---|---|---|
Max Pipe Size | ≤ 2″ | No upper limit | ≤ 4″ (practical) |
Welding Preparation | No bevel, just clean the pipe end | Beveling and alignment required | No welding needed |
Leakage Risk | Low | Very low | Medium (threads can loosen) |
Assembly Skill Requirement | Moderate | High | Low |
Disassembly / Maintenance | Difficult | Very difficult | Easy |
Susceptibility to Crevice Corrosion | Medium (gap at socket) | Low | Medium (threads) |
Common Standards | ASME B16.11 | ASME B16.9 | ASME B16.11, B1.20.1 |
Installation Tips
- Always clean pipe ends and the socket bore to remove oil and debris.
- Maintain a small gap (1/16″ or 1.6 mm) between the pipe end and the socket bottom to allow for thermal expansion.
- Use proper welding procedures and qualified welders.
- Inspect all welds visually and, if required, by non-destructive testing (e.g., dye penetrant).
Frequently Asked Questions (FAQ)
Q1: What standards define the dimensions and tolerances of socket weld fittings?
A1: The most common reference is ASME B16.11, which specifies dimensions, pressure ratings, and marking requirements.
Q2: When should I avoid using socket weld fittings?
A2: If the piping system needs frequent dismantling, or if the medium is highly corrosive and prone to crevice corrosion, butt weld fittings or flanged joints are generally better choices.
Q3: Are socket weld fittings suitable for hygienic or sanitary pipelines?
A3: Usually not, because the gap between the pipe and socket can harbor bacteria or residues. Hygienic systems prefer butt welds or special sanitary fittings.
Q4: What pressure ratings can socket weld fittings handle?
A4: Depending on size and schedule, socket weld fittings are typically rated for Class 3000, 6000, or 9000 service.
Q5: Can stainless steel socket weld fittings be used in high-temperature applications?
A5: Yes, but always confirm material specifications (e.g., ASTM A182 F316) and design temperature limits with your supplier.
Need Help Choosing the Right Fitting?
At Haihao Group, we manufacture and supply a full range of forged socket weld pipe fittings, with material certificates and pressure testing records. If you have questions about selection, standards, or stock availability, our technical team is ready to assist.
Email: sales@haihaogroup.com