How many methods are there of producing pipe caps?
Pipe caps are essential components used to close the ends of pipes, providing protection against environmental factors and preventing leakage. There are several methods for producing pipe caps, each with distinct processes and characteristics. Below are the primary methods of production, along with their specific processes and the resulting attributes of the pipe caps.
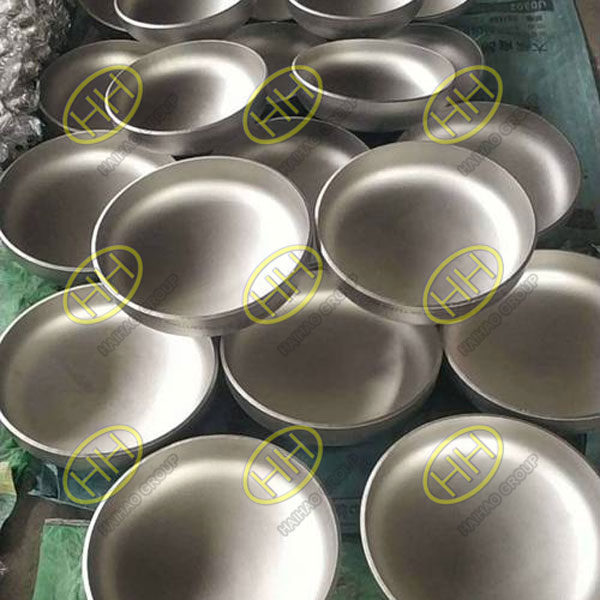
Pipe Caps
1.Forging
Process: In the forging process, metal is heated to a plastic state and then shaped using dies. The material is placed in a press, where it is subjected to high pressure to form the desired shape of the pipe cap. This method can be done either hot or cold, depending on the type of material used.
Characteristics:
Strength: Forged pipe caps have high mechanical strength and durability due to the refined grain structure achieved during the forging process.
Integrity: They exhibit excellent structural integrity, making them suitable for high-pressure applications.
Customization: Forging allows for customization in terms of size and design.
2.Welding
Process: Welded pipe caps are created by taking two flat metal plates and welding them together to form a cap. The welding can be done using various methods, including MIG, TIG, or stick welding, depending on the materials and required specifications.
Characteristics:
Versatility: Welding allows for the production of caps in various sizes and shapes, catering to specific project requirements.
Cost-Effectiveness: This method is generally less expensive than forging, especially for smaller production runs.
Potential Weak Points: Welded caps may have weaker joints compared to forged caps, making them less suitable for high-stress applications.
3.Stamping
Process: Stamping involves the use of a stamping press to cut and shape metal sheets into the desired cap form. The metal is placed into a die, where a punch is applied to create the cap.
Characteristics:
Efficiency: Stamping is highly efficient for mass production, allowing for the rapid creation of large quantities of pipe caps.
Uniformity: Stamped caps tend to have consistent dimensions and shapes due to the nature of the process.
Thickness Limitations: The thickness of the material used can limit the effectiveness of stamping.
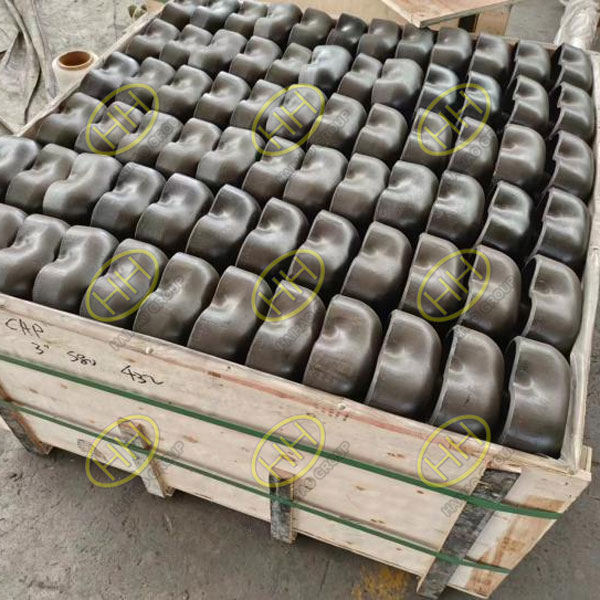
EN 10253-4 pipe caps
4.Casting
Process: Casting involves pouring molten metal into a mold, where it cools and solidifies into the shape of the pipe cap. This method can be used for both ferrous and non-ferrous metals.
Characteristics:
Complex Shapes: Casting allows for the production of intricate designs that might be challenging with other methods.
Material Diversity: A wide variety of materials can be used, including aluminum, brass, and iron.
Mechanical Properties: Cast caps may have lower mechanical properties compared to forged or welded caps, making them less suitable for high-stress applications.
5.Extrusion
Process: In the extrusion process, metal is forced through a die to create a long pipe cap shape. The extruded section is then cut to the desired length.
Characteristics:
Continuous Production: This method is efficient for producing long lengths of caps and can be used for both plastics and metals.
Consistent Thickness: The extrusion process ensures uniform thickness throughout the cap.
Limited Shape: Extrusion is generally limited to simpler shapes compared to forging or casting.
Each production method for pipe caps has its own advantages and disadvantages. Forged caps offer superior strength and integrity, making them ideal for high-pressure applications. Welded caps provide versatility and cost-effectiveness for various sizes, while stamped caps excel in efficiency for mass production. Cast caps allow for complex shapes but may lack the mechanical properties required for high-stress situations. Lastly, extrusion is a continuous process suitable for simpler designs.
When choosing a production method, it’s essential to consider the specific requirements of the application, including pressure ratings, material compatibility, and cost-effectiveness. Understanding these differences will help in selecting the most appropriate method for producing pipe caps.