Forming process of marine reducer
The manufacturer of marine reducer usually adopts the forming process of reducing diameter and expanding diameter pressing,expanding diameter pressing or reducing diameter pressing,and can also adopt stamping forming.
Stamping forming process is mainly aimed at the size of part of the special specification requirements of the reducer, the shape of the punch used for stamping can refer to the reducer of the internal surface design, with the punch will be blanked steel sheet stamping stretch forming. In order to solve the problem that the reducer is too large to be formed by reducing the reducer, the tube billet less than the diameter of the big end of the head is adopted, and the tube billet is formed by expanding the diameter along the inner diameter of the tube billet with an internal die. The shrink forming of reducer is to put the tube billet with the same diameter as the big end of reducer into the forming die, and then make the metal move along the die cavity and shrink forming by pressing along the axial direction of the tube billet.
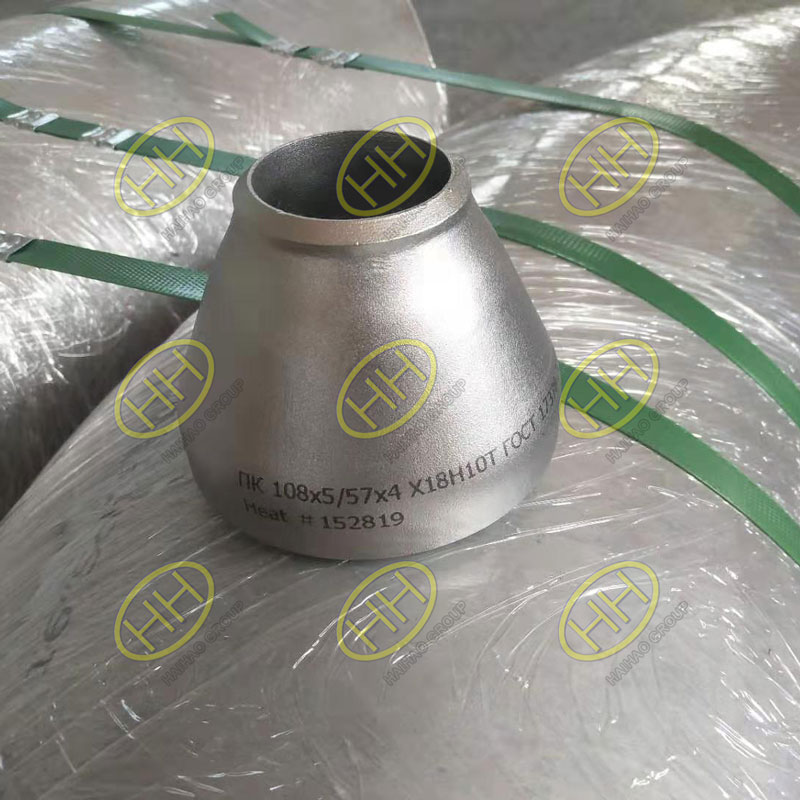
Concentric Reducers
Due to the size of the reducer change diameter,so the shrinkage forming can also be divided into one or more pressing forming.Sometimes according to the material and product forming needs,the method of expanding diameter and reducing diameter are combined.In the process of shrinking or expanding diameter deformation and pressing,according to different materials and diameter,determine the use of cold pressure or hot pressure. Generally, cold compression is used as far as possible, but for many times to change diameter and cause serious hardening of the case, the thickness of the wall slants thick or alloy steel materials, the reducer should be made by hot compression.
Welcome the new and old customers who are interested to come to exchange the relevant knowledge about the marine reducer process, Haihao Group with professional knowledge, advanced equipment and rich experience to serve you.Email:sales@haihaogroup.com