Welding process method of surfacing
There are there welding process methods of surfacing:oxyacetylene surfacing,electrode arc surfacing and submerged arc surfacing.Let’s see the process of surfacing:
1.Oxyacetylene surfacing
It is mainly used for surfacing of parts with smooth surface and high quality requirements, mainly for small and medium-sized weldments. Such as valve, oil well bit, plowshare and other parts of the surfacing.
Oxygen acetylene equipment is simple, easy to operate and low cost, which can be used in general with gas welding equipment, but the welding nozzle aperture of welding torch is larger than that of gas welding; almost all shapes of surfacing materials can be used (including leftover materials); the visibility is large, it can carry out surfacing on a small area, and it can get a thin and smooth surfacing layer; the dilution rate of this method is low, The depth of the melting layer can be controlled within 0.1mm, which is easy to guarantee the quality of the surfacing layer; the carburizing effect of the reduction flame can reduce the toughness of the surfacing layer, but it can improve the wear resistance of the surfacing layer with carbide as the main anti-wear phase; this method has a large labor intensity, low production efficiency, and certain technical requirements for welders.
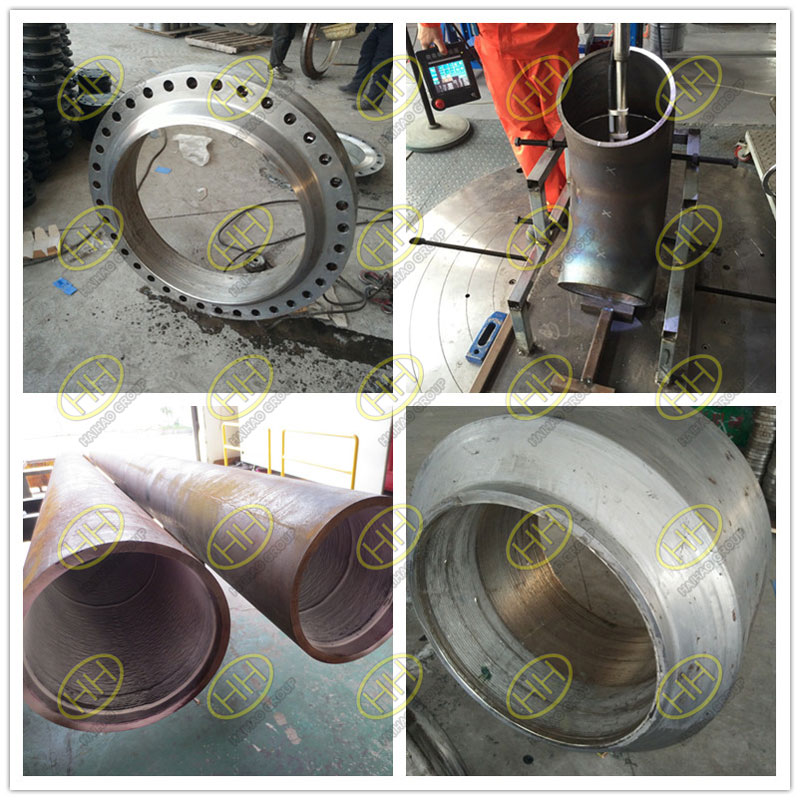
Weld Cladding Piping Products
Carbon flame is generally used for surfacing of o-acetylene. The flame property is related to the type of surfacing metal: neutral flame is usually used for nickel base alloy, but in order to improve the metal fluidity, carbon flame is occasionally used; double acetylene excess flame is used for surfacing of iron base alloy (the length ratio of internal flame to flame core is 2:1); low melting point surfacing alloy (such as high chromium cast iron or cobalt base alloy) with high carbon content is used for surfacing, Use 3 times of acetylene excess flame.
The vast majority of steel parts can be hardfacing without flux. Flux must be used when hardfacing cast iron. Meanwhile, measures should be taken to prevent white structure and crack. Preheating and slow cooling can greatly reduce the possibility of weld overlay cracking, and also help to reduce the dilution rate; small workpieces can be directly heated by welding torch, while large workpieces are generally heated in the furnace, and there is enough time to make the temperature uniform. The maximum thickness of each weld overlay is about 1.6mm, which can be multi-layer weld overlay.
The oxy acetylene spray welding (spray welding) is carried out with self fluxing alloy powder. According to the different sequence of powder spraying and remelting, the spray welding process is divided into “one step” and “two step”; the feature of “one step” spray welding is that powder spraying and remelting are carried out at the same time, that is, the method of spraying while melting. Generally, powder spraying is very fine, and its steps are preheating, pre spraying, spraying working powder and melting; “two step” Spray welding is characterized by two steps of powder spraying and remelting, which are preheating, powder spraying and remelting.
The common defect of oxyacetylene surfacing is that the pores are not fused, which is caused by improper operation or poor quality of surfacing material.
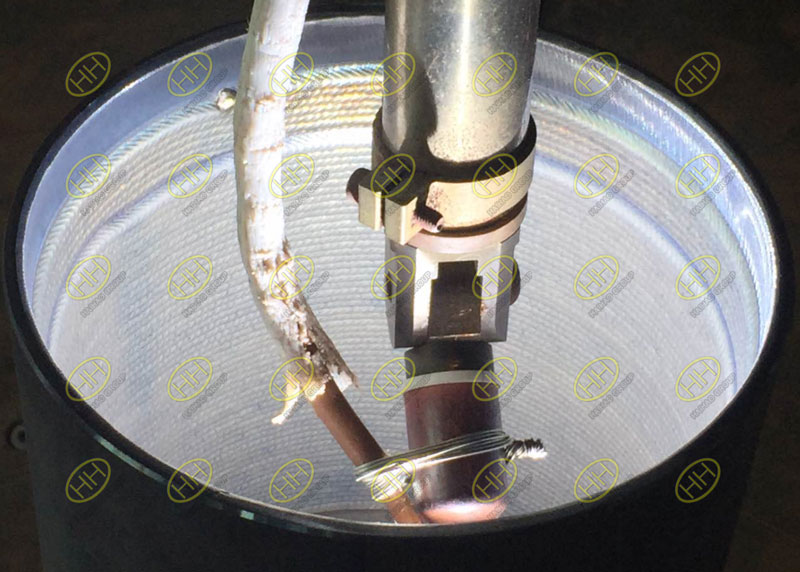
Weld Cladding Process
2.Electrode arc surfacing
The welding rod arc welding equipment is low-cost and versatile, which is suitable for on-site welding. The common power sources are: arc welding transformer, arc welding rectifier, arc welding generator and arc welding inverter, etc.; it is especially suitable for parts with irregular shape and parts with poor accessibility; the arc heat is concentrated, the deformation is small, and the productivity is high, but its penetration depth is large, the dilution rate is high, and the hardness and wear resistance of the welding layer are reduced, usually 2-3 layers are welded, Multi layer welding is easy to crack. Electrode arc surfacing is mainly used for small batch production and repair of worn parts. In China, there are: D10 × – 24 ×; D25 × – 29 ×; d30 × – 49 ×; D50 × – 59 ×; D60 × – 69 ×; D70 × – 79 ×; D80 × – 89 ×, etc.
The electrode of titanium calcium type, ilmenite type and low hydrogen type is better to adopt DC reverse welding for surfacing, while the electrode of graphite type is better to adopt DC Positive welding or AC power supply for surfacing. Before welding, the welding rod shall be dried with reference to the temperature specified in the welding rod manual. Generally, the acid welding rod shall be dried at 150 ℃ for 0.5-1h, and the alkaline welding rod shall be dried at 250-350 ℃ for 1-2h. The preheating temperature of surfacing welding is mainly determined according to carbon equivalent, for example, carbon equivalent (%) is 0.4, 0.5, 0.6, 0.7 and 0.8, and the preheating temperature (℃) is 100, 150, 200, 250 and 300 respectively. The slow cooling after surfacing can be carried out in furnace or asbestos, or it can be cooled slowly by proper heating.
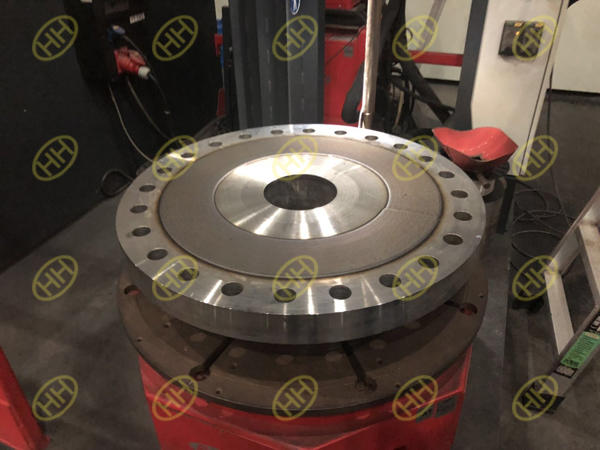
Nicked alloy cladding flanges 825 alloy material weld overlay on the base material ASTM A335 P11
3.Submerged arc surfacing
Submerged arc welding is automatic production, high current, high efficiency; no light radiation, good working conditions; submerged arc heat has a large dilution rate, generally 23 layers of welding can ensure the required performance, in order to avoid cracking, preheating and slow cooling measures are often taken; mainly used for horizontal position welding, which is most suitable for the welding of large and non deformable parts, such as the inner wall of large-diameter vessels, It is not suitable to overlay small parts on the roll of rolling mill.
DC power or AC power can be used for submerged arc welding. In order to improve the quality and production efficiency of welding, most of them adopt DC reverse connection. If the welding current is increased, the dilution rate, penetration and thickness of the welding layer will be increased. The influence of the welding arc voltage on the dilution rate is not obvious. Generally, 30-35v arc voltage is selected, Generally, the extension length of welding wire is 8 times of the diameter of welding wire; in order to reduce the dilution rate and improve the deposition speed, the electrode adopts the improvement methods such as multi wire, band electrode (in series and parallel) and so on. Other surfacing methods include: GMA surfacing, TIG surfacing, plasma arc surfacing, electroslag surfacing, laser surfacing, friction surfacing, etc.
As a professional pipeline supplier,we can supply clad pipe fittings,clad flanges and clad pipes in different welding process.If you want to know more about our products,please feel free to contact us.Email:sales@haihaogroup.com