How to select the right pipe fitting size for your system
Choosing the correct pipe fitting size and pressure rating is essential for the safe, efficient, and reliable operation of any piping system. Whether you’re designing a new installation or replacing worn components, understanding key concepts such as NPS, pipe schedule, pressure class, and proper matching of fittings to pipes will help you avoid costly mistakes.
NPS and DN: Translating Nominal Pipe Sizes
In North America, pipes are identified by Nominal Pipe Size (NPS), a designation that loosely corresponds to the pipe’s internal diameter in inches. In metric regions, you’ll encounter Diameter Nominal (DN), which roughly represents the pipe’s internal diameter in millimeters. For example, NPS 2 corresponds to DN 50. Keep in mind that these are nominal values—actual internal and external diameters vary with pipe schedule. Always consult dimensional charts or manufacturer data to confirm precise measurements.
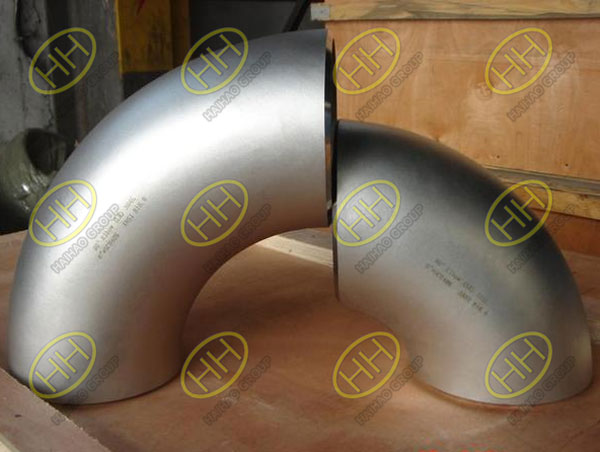
ASME B16.9 90 degree elbow SR BE ASTM A234 GR WPB seamless butt welding SCH40
Pipe Schedule: Wall Thickness and Flow Capacity
The pipe’s schedule number (such as Schedule 40 or Schedule 80) indicates its wall thickness. A higher schedule means a thicker wall, which translates into higher pressure capability but slightly reduced flow area. When selecting fittings, it’s vital to match the fitting’s bore and wall thickness to the schedule of your pipe. Mixing a Schedule 40 fitting on a Schedule 80 pipe, or vice versa, can result in misalignment, poor weld or thread quality, and potential leakage.
Pressure Rating: Choosing the Right Class
Pipe fittings are also rated by pressure classes, commonly Class 150, 300, 600, and higher. A Class 150 fitting is designed for moderate pressures—up to about 285 psi at ambient temperature—while Class 300 can handle pressures up to roughly 740 psi. As you move to Class 600, 900, and above, fittings become suitable for increasingly demanding high-pressure and high-temperature services. Always select a fitting whose class rating meets or exceeds the maximum expected operating pressure and temperature of your system.
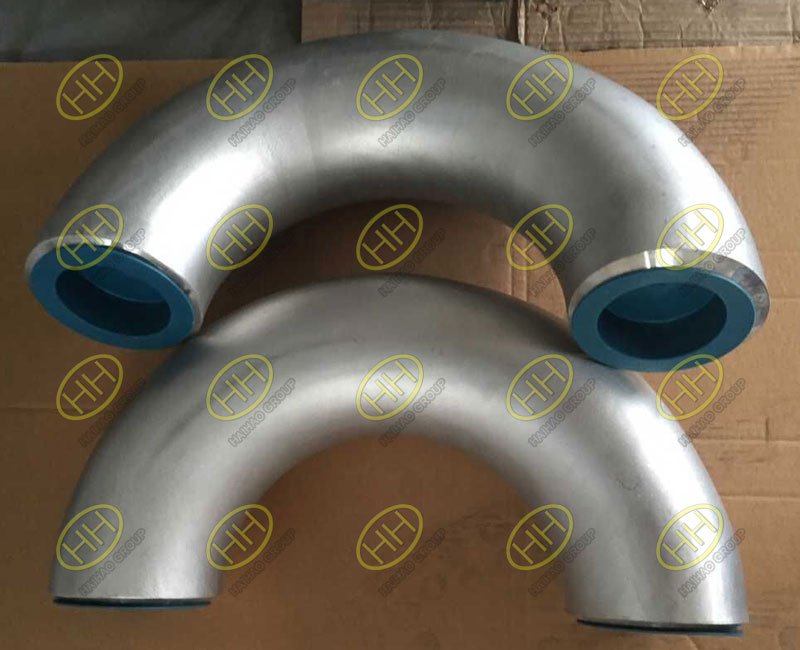
Stainless steel butt weld 180 degree elbows finished in Haihao Group
Matching Fittings to Pipes: Connection Types
There are three primary methods for joining small- to medium‑diameter pipes:
Threaded fittings screw directly onto NPT‑threaded pipe ends. They’re quick to install and cost‑effective for low-pressure or temporary systems, but they are more prone to leakage if overtightened, subjected to vibration, or used in corrosive environments.
Socket‑weld fittings require the pipe to be inserted into a machined cavity and fillet‑welded in place. This connection yields a stronger, more leak‑resistant joint than threading and is well suited to high‑pressure applications up to 4 in. diameter.
Butt‑weld fittings involve beveling the pipe ends and welding them together, creating a smooth, full‑penetration joint. This method is preferred for larger diameters and systems under high pressure or temperature, offering superior flow characteristics and mechanical strength.
Common Selection Pitfalls
Assuming Nominal Size Equals Actual Dimension
NPS and DN are nominal only. Always verify actual inside and outside diameters for both pipe and fitting before installation.
Mismatched Schedules
Don’t pair a fitting made for one pipe schedule with a different schedule pipe. Wall thickness differences can lead to poor welds or loose threads.
Underrated Pressure Class
Selecting a Class 150 fitting for a system that regularly operates near or above 285 psi can risk gasket failure or flange blow‑out. Match the fitting class to the highest expected system pressure and temperature.
Incompatible Connection Types
Mixing thread types (e.g., NPT with BSP) or using the wrong fitting style for the service may cause leaks and complicate maintenance.
Ignoring Application Conditions
Factors such as vibration, corrosive media, and temperature extremes must be considered when choosing threaded versus welded connections.
By carefully considering NPS versus DN, pipe schedule, pressure class, and the appropriate connection method, you’ll ensure a proper fit, reliable seal, and long service life for your piping system. Thoughtful selection now keeps your installation running smoothly for years to come.