Differences between Type A, Type B, and Type C stub ends
Stub ends are essential components in piping systems, primarily used to facilitate connections with lap joint flanges. Among the various types of stub ends, Type A, Type B, and Type C stub ends are the most common, each designed for specific applications and pressure requirements. This article will explore the key differences among these three types of stub ends.
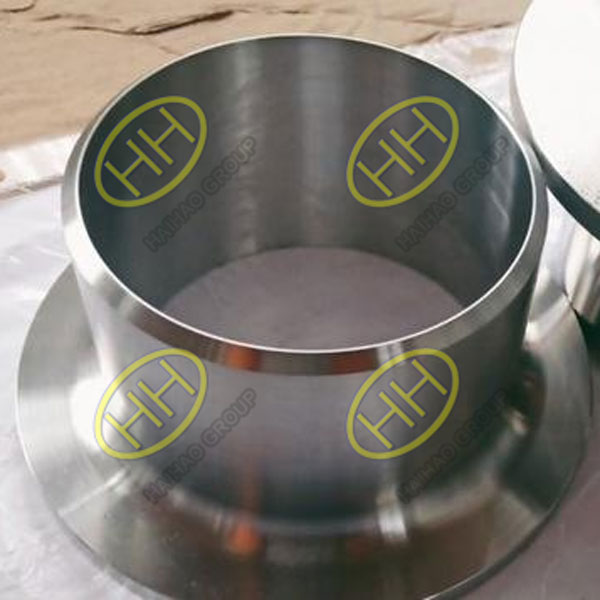
Stub End
1.Type A Stub End
Design:
Type A stub ends are characterized by their long tapered hub, which ensures a smooth flow transition. The curved radius aligns with the bore of the pipe, helping to minimize turbulence and erosion at the joint.
Applications:
Type A stub ends are typically used in low to medium-pressure piping systems. They are ideal for applications where connections with lap joint flanges are required.
Key Features:
Provides flexibility in alignment during installation.
Compatible with a wide range of flanges, making it easier to adjust positions as needed.
Commonly manufactured from materials such as carbon steel and stainless steel.
2.Type B Stub End
Design:
Type B stub ends feature a shorter, less tapered edge that is closer to the diameter of the pipe. This design provides a more robust connection, suitable for higher pressure applications.
Applications:
These stub ends are often employed in systems that require higher strength and pressure capabilities. They are suitable for high-pressure environments where safety and reliability are critical.
Key Features:
Higher pressure ratings compared to Type A stub ends.
Requires stricter flange specifications for compatibility.
Can sometimes be used as a replacement for Type A, depending on the application needs.
3.Type C Stub End
Design:
Type C stub ends are defined by their short, straight edges without any tapering. This design allows for a different method of connecting to flanges, which can be beneficial in specific situations.
Applications:
Type C stub ends are typically used in extreme environments, such as high-temperature and high-pressure systems. They are often found in industries such as oil and gas, chemical processing, and power generation.
Key Features:
Offers greater flexibility in connection methods.
Suitable for applications where unique flange types or connections are needed.
Generally made from high-strength materials to withstand demanding conditions.
Conclusion
The distinctions between Type A, Type B, and Type C stub ends lie in their design, pressure ratings, and specific applications.
Type A Stub end provides smooth flow transitions and is ideal for low to medium-pressure systems.
Type B Stub end is suited for higher pressure applications with stricter flange requirements.
Type C Stub end is designed for extreme conditions, offering flexibility in connections.
Understanding these differences allows engineers and designers to select the appropriate stub end type for their piping systems, ensuring optimal performance and safety in various applications.